Sliced veneer — manufacturing standards and technology
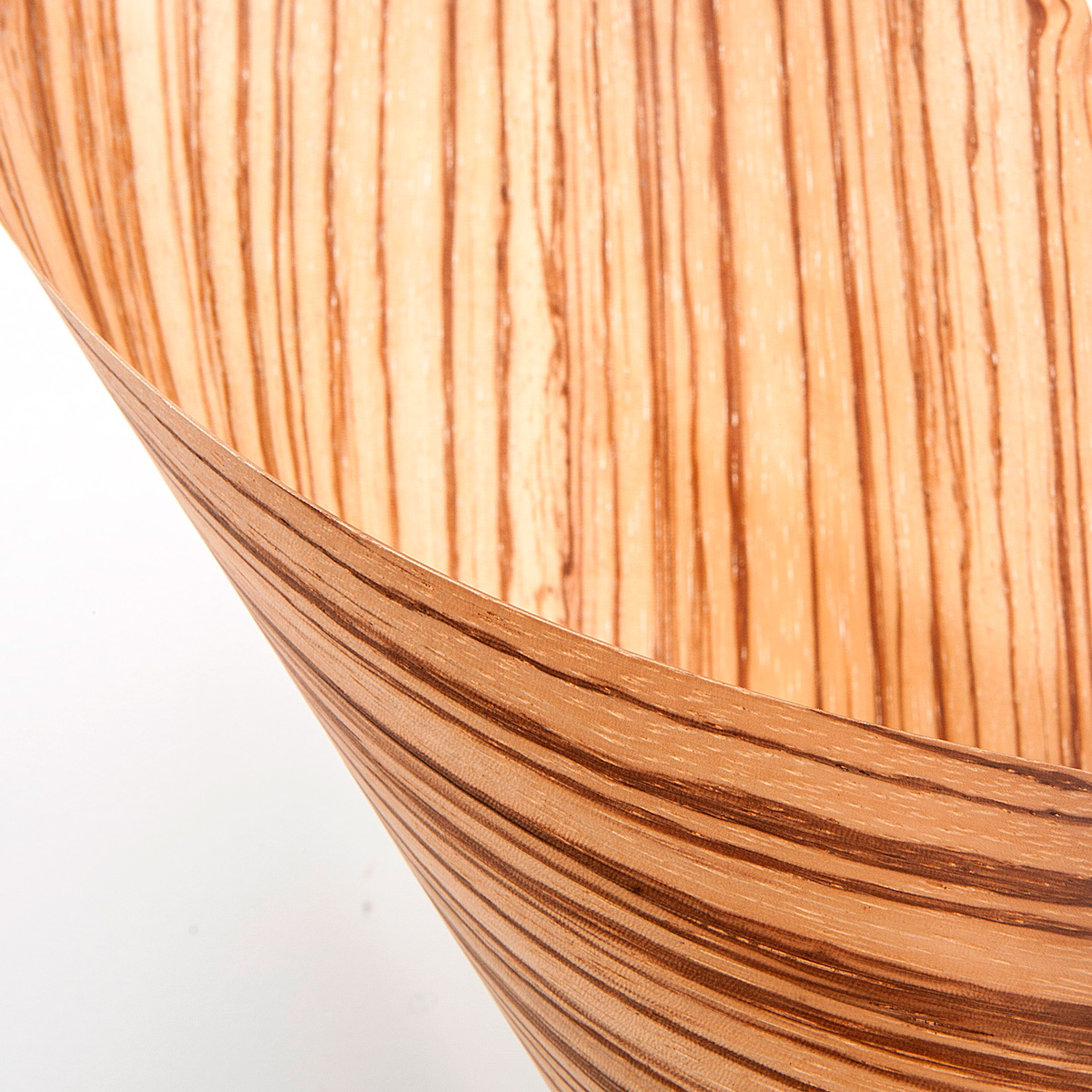
Sliced veneer must be manufactured in accordance with the standards of the process instruction approved in the prescribed manner. Standard GOST 2977-82 applies to sliced veneer, which is used as a cladding material.
Veneer of class I and class II
Veneer quality wood veneer divided into first class and second class veneer. Grade veneer is determined by the presence of certain defects of wood.
Veneer of the first grade is mainly of minor defects, allowed:
- Healthy Intergrown light and dark knots up to 20 mm per 1 m length of the sheet;
- Allowed fungal destruction, but shall not exceed 10% of the area of the sheet, it can be brown, mushroom dyeing, mushroom stripes and spots;
- Allowed 10% of the area of the sheet of chemical coloring;
- No more than 10% of the area of the sheet permissible internal sapwood and spotting.
For veneer of the second grade according to GOST-standard allowed more wood defects, so the life of the veneer is less long, and the aesthetic appearance is less attractive.
Euroshpon-Trade offers you sliced veneer different types of wood at affordable prices and decent quality. We are always glad to cooperation and we offer the best conditions to our partners and clients.
Depending on the wood texture according to GOST-standard veneer is divided into the following types:
Veneer type | Characteristics of veneer species | |
---|---|---|
By annual layers | By core rays | |
Radial (R) | Year layers as straight parallel lines along the entire surface of the sheet | Core rays have the form of strips arranged at least on ¾ sheet area |
Half radial (HR) | Layers in the form of direct parallel lines located not less than ¾ square sheet | The rays have the form of inclined or longitudinal strips located not less than ½ square sheet |
Tangential (T) | Annual layers in the form of a cone of increase, angles or curved lines | The rays have the form of longitudinal or oblique strokes or lines |
Tangential end face (TF) | Year layers have the form of closed curves | The core rays appear as curved lines or strokes |
Dimensions of sliced veneer class 1 and 2, according to GOST 2977-82:
Size sheet | 1st grade | 2nd grade | ||
---|---|---|---|---|
T, HR, R | TF | T, HR, R | TF | |
Minimum length (with gradation 50) | 900 | 200 | 400 | 200 |
Minimum width (with gradation 10) | 120 | 200 | 160 | 100 |
Thickness | 0,5; 0,6; 0,7; 0,8; 0,9; 1,0 |
However, the humidity of the wood should match the rate — 8 (±2%).
Characteristics of wood for the production of sliced veneer:
Tree species | Raw material grade | Diameter, not less than (cm) | Length, not less than (m) |
---|---|---|---|
Oak, ilm, beech, ash | 1; 2 | 26 | 1,5 |
Maple, walnut, velvet, hornbeam | 1; 2 | 22 | 1,5 |
Mahogany | 1; 2; 3 | 40 | 3,0 |
Larch | 1; 2 | 32 | 2,5 |
Technological process of obtaining sliced veneer
To obtain high-quality veneer should take a responsible approach to each stage of its manufacturing process, from preparation to sliced. For cross-cutting of wood electric saws or gasoline-engine saws are necessary. Usually such cutting is necessary if the length of logs exceeds 3 meters. For longitudinal cutting band saw vertical and horizontal machines are used in production of an interline interval. Cutting can give a symmetrical parallel bars and asymmetric bars (wanchese).
There are a lot of methods of longitudinal cutting, and their choice depends on:
- Output radial veneer;
- Diameter of wood;
- Number of sliced bars (simultaneous process);
- Fastening of asymmetric bars.
Methods of cutting wood and their characteristics:
- «Wanchese» 4-way — receive a high quality veneer, sliced goes from the center to the periphery. Often this method is used for mahogany beams;
- Cut into quarters-radial veneer is obtained, the sliced of the bars takes place in two stages;
- «Kryazhevoy» method — you need reliable fastening of the materials that they receive the tangential veneer;
- Method of tripling with sawing core board-use, if there are problems in the quality of raw materials, namely the core of wood, often used for such wood as larch;
- Triage without sawing core-get radial veneer, but the process of sliced is more time-consuming;
- Lumber blunt mode way — need a reliable fasteners, receive a tangential veneer;
- Combined method of cutting-suitable for wood with tread cracks and bars of large diameter;
- Asymmetrical cutting for beams with an oval cross-section;
- Sector-radial method is applied to blanks by piece, is laborious, but in the end get high quality veneer (up to 70% radial veneer);
- «Wanchese» with cutting out the core wood used for larch or material defects in the region of the core.
For further stage of production of veneer used sliced-veneer vertical, horizontal and slant machines. Stages of work on the machine are as follows:
- Bars are loaded on the working surface of the machine, installed with fasteners;
- Process of sliced and issue of sheets;
- Laying of veneer, obtained from a single beam in a bundle;
- Re-routing of bars;
- Sliced after recanting of «wanchese»;
- Removes the remaining after sliced the fillets.
Production sliced veneer is a time-consuming and unique process. When veneering in the furniture industry it is very important that the material was of the highest quality, the only way to get aesthetically beautiful products, so buy sliced veneer is recommended from a trusted manufacturer. The company Euroshpon-Trade is a representative of Euroshpon-Smyga and is responsible for product quality and compliance of veneer GOST standards.